2018 is waning and 2019 is on the horizon.
I like to take the last few days of the year to clean and organize so I can get a fresh start in the new year. It is also a time to look back at my accomplishments or failures and to reassess my goals for the new year.
2018 was, overall, a good year for me. Although some negative things forced changes, the changes were for the better. One example is, our heating and air-conditioning system was getting old and was due to be replaced. When we had our annual cleaning and inspection the service man found that there were a few issues and suggested we should replace them. We knew it was only a matter of time and the time was now. In addition to replacing the heat pump and AC units we decided to change from an electric supplemental to propane. And, while we were putting in the propane, we might as well get the generator we had been discussing.
Another big change was purchasing a new wheelchair accessible van. My husband uses a wheelchair and it has been getting more difficult to transfer into our car, so the van was needed. It has been so much safer and easier with the van.
Now, on the weaving side, I got an AVL A-series 40" 24 shaft Compu Dobby loom. This was something I never seriously thought about until earlier this year. The cost was more than I would ever expect to spend on something for myself. I was so happy when my husband said to get it. I love my new loom. I am learning more and more about weaving and that makes me happy.
With so many major items this year I am hoping 2019 won't require much in the way of maintenance.
As far as my goals for 2019, I am hoping to exercise more, drink more water, spend more time weaving and working outside in my yard and gardens. I would like to spend more time enjoying the present and not worry about the future.
I think my goals are attainable so I should have a fantastic New Year.
Friday, December 28, 2018
Friday, December 14, 2018
Weaving a Rainbow
If you can't decide on a color, use them all!
I enjoy bright colors and this warp makes me happy. I warped my HD loom with 8 yards of 8/2 Tencel to weave several scarves. The threading is an 8 shaft straight draw so I can use several twill drafts to make each scarf slightly different.
Are you familiar with Tencel?
Tencel is one of my favorite threads with which to weave. It has a beautiful sheen, comes in many colors, and makes a soft, silky fabric with a beautiful drape.Tencel is also known as Lyocell. It is made from the pulp of wood which is chemically treated to create a slurry which is pumped through spineretts to make a continuous filament. Tencel can be used by itself or mixed with other fibers.
Lyocell is used in many fabrics we use daily. It is wrinkle resistant, soft, absorbent and makes a strong fabric that will stand up to machine washing and drying as well as dry-cleaning.
I have only woven with silk a few times. The silk I used was close to the size of 8/2 Tencel. For me, the silk and Tencel are almost identical. The cost of Tencel is so much lower than silk that I think it is a great substitute for silk.
There are a few things to keep in mind when weaving with Tencel. It is slippery, so when you tie on to the apron rod make sure your knots are tight. Also, the selvedge threads have a tendency to wear and break.
To reduce the breakage there are several things to do. First, watch your draw-in. If possible, use a temple, an end-feed shuttle and beat on an open shed then close the shed before pushing back on the beater. When you beat on an open shed the weft will ease into the warp better and not pull on the edges. Then, close the shed before moving the beater back. This will hold your last pick where it belongs while you change the shed. Since Tencel is slippery, it has a tendency to bounce back away from the fell if you don't trap it with the next shed.
When you take your fabric off the loom you will find it seems hard and has no drape. Don't despair. Once you wash it the fabric changes. The next step is to press it with a hot iron. I mean PRESS it. Hold the iron in one place and press down, move the iron to the next place and press down. Do this on both sides of the fabric then Iron the entire piece by moving the iron back and forth. The ironing sort of polishes the fabric. You only need to do this pressing to finish the weaving process. For future cleaning a light ironing is all that may be needed.
Tuesday, December 11, 2018
24 Shaft Design
What I love about my AVL Loom is the intricate designs that can be woven with 24 shafts. By using 24 shafts it enlarges the scale of the pattern woven, Technically, if the pattern is sett at 24 ends per inch and it is repeated as a point twill, the pattern should be 2 inches. Because of draw-in the design is slightly smaller than 2".
The challenge with an obviously square design is beating it so it is square. I am using 8/2 Tencel sett at 24 EPI. My natural beat is closer to 27-30 Picks Per Inch which would make the design shorter than wide. It takes some concentration to get the beat light enough to be 24 EPI.
I could sett the Tencel closer which would make beating it square easier, but that would create a stiffer fabric. Since I want this to be a scarf and have a nice drape I chose 24 EPI.
This draft is #29521 from Handweaving.net. This is a website with a collection of drafts and documents written about weaving. You may browse the site for free. When you purchase an annual subscription for $20. you can download WIF files of the drafts. There are drafts from 2 shafts up to at least 36 shafts.
Handweaving.net is a fantastic source of drafts as well as documents which include entire books like Peter Collingwood, The Techniques of Rug Weaving and many short articles on multiple subjects.
Friday, December 7, 2018
Warp Gradation: Using Fiberworks to create a gradient.
Gradation of colors in the warp can create a very interesting background for a pattern.
When using Fiberworks software select "Colors" from the band at the top of the screen then choose "Create Gradient". A box will appear giving you several selections.
- Choose the color you want to start with from the color bar then pick the color to end with.
- Select how many colors you want to blend. The more colors you choose, the more gradual the gradient will be.
- Number of threads. If you want the color to change across the entire warp choose the total number of warp threads. If you want to mirror the color, like the photo above, divide the total number of ends in half and insert that number. Example: 200 total warp ends would be 100 for half the warp.
- Click on "Add to end", this will place the color on the draft. If you selected half of the total warp the color will only fill in half of the draft.
- To finish the mirror effect click add to end again. This puts the color on the other half of the warp but it needs to be reversed to give you the mirror.
- Click "Reverse" and you should have the mirror effect across the entire warp.
The computer will give you an endless number of colors, however, you need to check how many colors of thread you have to create the gradient. You may need to decrease the number of colors in the program to make it practical for the colors you have on hand.
Just follow the threading sequence to get a nice gradation. This does take time when warping but it gives a beautiful warp at the end.
Something to consider when creating a gradient is the draft you will be using. When you take a lot of time to create a beautiful warp the draft should highlight the warp. You could choose a warp dominant draft or a draft with a simple design.
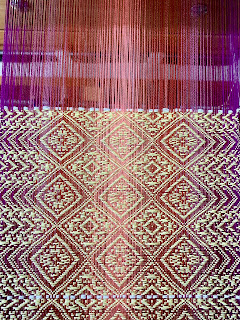
The draft I chose for this gradient is too dominant and hides the gradient. I tried several colors of weft and eventually picked yellow because I wanted to highlight the design. I now wish that I had not done the gradient for this draft; as it does not show in the finished cloth. In the future I need to decide in advance which aspect is more important and will choose a draft that is more appropriate.
I also think that the scale of this project is too small for the gradient. This is about 9 inches wide for a scarf. I think something wider would be better for the gradient.
The scarf is still beautiful but is not exactly what I envisioned for this warp.
Tuesday, December 4, 2018
Single Fly Shuttle... Stopping it from flying off.
This is my first experience with a fly shuttle.
I have a single box fly shuttle. This means that it uses only one shuttle. There are double and Quad fly boxes available so you can weave with multiple shuttles. I decided a single would be used the most.
My loom is 40" wide. I am 5ft 1inch tall and have short arms. When weaving full width on my HD 36"loom I could not throw the shuttle across easily, so I decided to get a fly shuttle for the 40" loom. Besides, I wanted to play with one.
It is important that you have the shuttle box even with the shuttle race on the beater so that the shuttle runs smoothly from the race into the box and vice versa. I am familiar with using an end feed shuttle and love them. When I switched from a boat shuttle to an end feed shuttle my broken selvedge threads stopped and the selvedge was nice and smooth. The shuttle for the fly has metal on the tips and is a little heavier than my other EF shuttles.
I was hesitant to use the fly shuttle. All I could imagine was the shuttle sailing off the loom and through the picture window near the loom. The first few pulls were too light to get the shuttle from one box to the other. With a little practice I was doing it well.
With the warp on the loom and thread in the shuttle I started again. Klunk, the shuttle fell off the right side of the loom and hit the floor. I got a small rug and put it under the loom to protect the hardwood floor and tried again. It fell a few more times, I could not figure out what I was doing wrong.
I asked on Warped Weavers on Ravelry.com and Bonnie Inyone suggested turning the shuttle around so that the Honex feeder was toward the reed. Like magic, it worked.
As I look at it now I understand why. As you throw the shuttle from the left to the right the thread catches the left selvedge. This starts to pull the right tip of the shuttle, where the Honex feed was, away from the reed. When it gets to the metal guide near the right box it hits the outside edge and causes it to fall outside the box to the floor.
When you turn the feed toward the reed it does not pull the tip of the shuttle out and it sails into the box with ease.
One more tip. Get a good paste wax and wax the shuttle race, fly box and the shuttle. It reduces the drag and makes using the shuttle easier. This is something that should be done as routine maintenance.
Using the fly shuttle gives me a very nice selvedge and is quicker than throwing the shuttle. The only disadvantage is that it does not allow for the use of a floating selvedge. When using a twill draft I will need to thread a basket weave or plain weave on a couple shafts to get a selvedge without floats along the edge.
I have a single box fly shuttle. This means that it uses only one shuttle. There are double and Quad fly boxes available so you can weave with multiple shuttles. I decided a single would be used the most.
My loom is 40" wide. I am 5ft 1inch tall and have short arms. When weaving full width on my HD 36"loom I could not throw the shuttle across easily, so I decided to get a fly shuttle for the 40" loom. Besides, I wanted to play with one.
It is important that you have the shuttle box even with the shuttle race on the beater so that the shuttle runs smoothly from the race into the box and vice versa. I am familiar with using an end feed shuttle and love them. When I switched from a boat shuttle to an end feed shuttle my broken selvedge threads stopped and the selvedge was nice and smooth. The shuttle for the fly has metal on the tips and is a little heavier than my other EF shuttles.
I was hesitant to use the fly shuttle. All I could imagine was the shuttle sailing off the loom and through the picture window near the loom. The first few pulls were too light to get the shuttle from one box to the other. With a little practice I was doing it well.
With the warp on the loom and thread in the shuttle I started again. Klunk, the shuttle fell off the right side of the loom and hit the floor. I got a small rug and put it under the loom to protect the hardwood floor and tried again. It fell a few more times, I could not figure out what I was doing wrong.
I asked on Warped Weavers on Ravelry.com and Bonnie Inyone suggested turning the shuttle around so that the Honex feeder was toward the reed. Like magic, it worked.
As I look at it now I understand why. As you throw the shuttle from the left to the right the thread catches the left selvedge. This starts to pull the right tip of the shuttle, where the Honex feed was, away from the reed. When it gets to the metal guide near the right box it hits the outside edge and causes it to fall outside the box to the floor.
When you turn the feed toward the reed it does not pull the tip of the shuttle out and it sails into the box with ease.
One more tip. Get a good paste wax and wax the shuttle race, fly box and the shuttle. It reduces the drag and makes using the shuttle easier. This is something that should be done as routine maintenance.
Using the fly shuttle gives me a very nice selvedge and is quicker than throwing the shuttle. The only disadvantage is that it does not allow for the use of a floating selvedge. When using a twill draft I will need to thread a basket weave or plain weave on a couple shafts to get a selvedge without floats along the edge.
Subscribe to:
Posts (Atom)